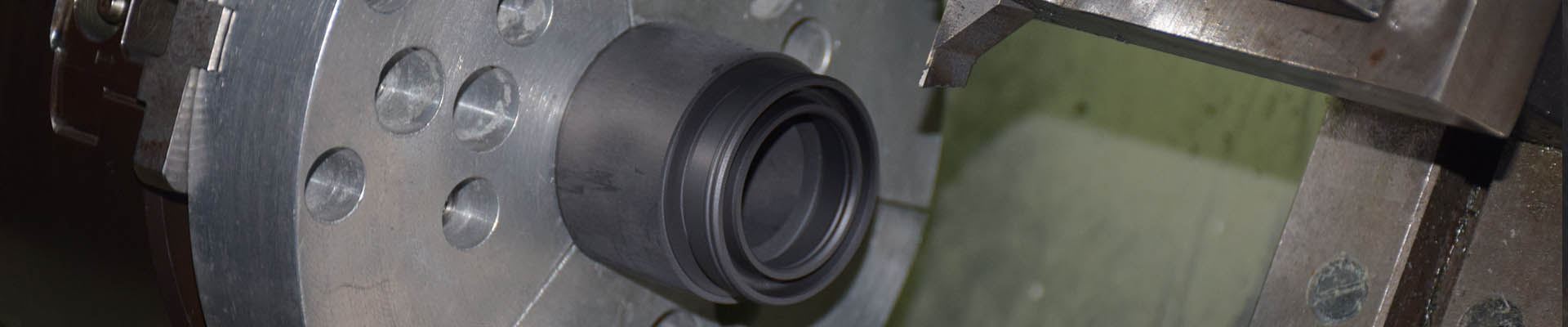
Application analysis of rubber O-ring in ball valve
As one of the main components of valves and pressure pipelines, pressure dissolvers, boilers and other equipment, ball valves are used to control the flow or cut-off of media. They are widely used in various industries such as LNG, electric power, light industry, construction, metallurgy and so on. As a low cost, rubber O-ring (hereinafter referred to as O-ring) is applicable to be installed in various valves to provide sealing protection under static or dynamic conditions under specified temperature, pressure and different liquid and gas media. When the ball valve is in the closed position, the specified sealing requirements (or leakage requirements) shall be met. In the design, the O-ring is selected as the sealing element, which can successfully prevent leakage and achieve complete sealing effect. Especially, when the valve stem rotates during the opening and closing process of the ball valve, the movement friction of the O-ring is very small, and the O-ring is selected as the sealing element to achieve zero leakage. Therefore, O-ring is one of the most widely used sealing elements with the best sealing effect in ball valve.
1. Application scope
Ball valve is a kind of valve that can be opened and closed by manual drive device, pneumatic drive device or electric drive device under different working conditions. During the ball valve production, O-ring is a sealing element suitable for various sealing forms. Its dynamic sealing and static sealing play an important role in the sealing performance of various ball valves. Take the two-piece ball valve as an example, as shown in Figure 1. The O-ring on the end face and in the valve stem can effectively prevent the leakage of various media and ensure the normal operation of the valve system. When the O-ring is installed on both ends, it belongs to the static sealing effect. When the O-ring is installed on the middle hole of the valve body and the valve stem, it belongs to the dynamic sealing effect. Both sealing effects fully meet the design requirements of ball valves.
(1) Static seal
The O-ring belongs to the extrusion seal. The basic feature of the extrusion seal structure depends on the elastic deformation of the seal and the contact pressure on the sealing contact surface. When the contact pressure is greater than the internal pressure of the sealed medium, it plays a sealing role, and on the contrary, it leads to leakage. The left and right end bodies of the two-piece ball valve are in metal to metal contact and belong to a static sealing structure. In order to reduce or eliminate the sealing surface gap between them, the O-ring is selected as the sealing element in the design. When the medium pressure is small, it is in a static state and the required sealing force is very small. At this time, the left and right end bodies can be sealed by the pre tightening force during assembly and the elastic force of the O-ring; When the medium pressure keeps increasing, the sealing specific pressure also increases, and the O-ring suddenly expands. At this time, the O-ring effectively prevents the leakage point between the gaps at both ends, thus ensuring the sealing performance of the ball valve.
When the ball valve is opened and closed, no matter what driving mode is adopted, the valve stem will rotate. In order to prevent the medium from escaping through the middle hole gap, a groove is hooked on the valve stem and embedded into the O-ring. Although the valve stem rotates 90 ° reciprocally, due to the small friction and good self lubrication of the O-ring, they cooperate with each other to achieve good sealing effect. In order to ensure that the valve seat and the valve core form a good sealing performance, a groove is also machined in the valve seat and the O-ring is installed therein. When the pressure of the medium in the valve cavity rises, the valve seat will move toward the valve core under the urging of the spring force. Under the action of the high elastic performance of the O-ring, the tightness of the inner cavity of the pipeline is ensured. At this time, the O-ring starts the dynamic sealing effect in the pipeline. In the first two structural forms, the O-ring belongs to the dynamic sealing structure.
(3) Zero leakage seal
The sealing structure of the ball valve is divided into two structural types: metal sealing and soft sealing. Compared with the soft sealing structure, the leakage rate of the metal sealing structure is higher. According to the API valve leakage level, if the leakage level of the metal sealing structure should reach VI (equivalent to zero leakage), and the temperature should be less than 200 ℃. At this time, the O-ring is selected as the sealing member for both static and dynamic sealing ball valves, All design parameters are fully met. For the gas ball valve, in order to prevent the gas medium from leaking through various channels, causing flammability and explosion, O-rings are embedded at each leakage point, which can effectively prevent the leakage of the valve body. The clearance value is less than 0.001 μm. So it is especially suitable for special working conditions where gas, dust and other media are required.
2. Material selection
There are many kinds of O-ring materials, including fluororubber (FKM), nitrile rubber (NBR) and silicone rubber (VMQ), ethylene propylene rubber (EPDM), natural rubber (NR), HNBR, FFKM, etc. The commonly used O-ring materials in ball valves are generally fluororubber, nitrile rubber and silicone rubber. For ball valves requiring high temperature, such as ball valves above 200 ℃, it is recommended to select other types of sealing elements. The O-ring material used in the ball valve is not only related to temperature, medium and pressure, but also affected by the operating conditions, environment and various comprehensive factors.
(1) Temperature
Temperature is one of the main factors affecting the use range of O-rings. In the process of ball valve design, the applicable temperature of the selected O-rings is generally -29 ~ 180 ℃. For ball valves under high-temperature or low-temperature conditions, special synthetic materials shall be selected as seals to meet the requirements of sealing performance.
In common rubber materials, FKM has excellent high temperature resistance. The working temperature range of ordinary FKM is - 25 ~ 240 ℃, while the special brand of FFKM can withstand the constant temperature of 300 ℃ or the instantaneous high temperature of 340 ℃ without hardening and expansion failure. Therefore, for ball valves used under high temperature under other working conditions, FFKM can be appropriately considered.
Rubber will embrittle and lose sealing effect when used under low temperature conditions. Therefore, low temperature ball valves are generally not recommended. Silicone is one of the most low-temperature resistant materials in rubber materials. Although it can reach - 100 ℃, it has low tensile strength and poor wear resistance. Generally, it cannot be used for rotating dynamic sealing parts. Therefore, ball valves under low temperature conditions are not suitable for selection. According to relevant data, the service temperature of silicone rubber is - 60-220 ℃, which enhances the chemical resistance and mechanical properties on the basis of maintaining the temperature resistance of silicone rubber.
(2) Medium
As one of the five major valves, ball valves are applicable to different engineering industries. For different media, it is very necessary to select appropriate rubber materials and O-rings with appropriate materials. For example, FKM O-rings have flame resistance, good air tightness, ozone resistance and excellent corrosion resistance. Silicone O-ring is more suitable for ball valves with dust and particle media. Nitrile O-ring has good sealing and shock absorption in oil, acid, alkali, abrasion, chemical invasion and other environments. Therefore, suitable O-rings can be selected in the ball valve for other mixed chemical media such as acidic media, oil, water, gas, oxidizing and reducing media.
(3) Pressure
According to the chemical principle of O-ring; The hardness of the O-ring is generally shore 50-90. When the pressure pipeline of the valve is low, the O-ring with the hardness of shore 50-70 should be preferred for cost-saving and environmental protection. When the pressure pipeline of the valve is high, the O-ring with the hardness of shore 70-90 should be recommended for safety. When the pipeline pressure is greater than or equal to 150LB or 1.0MPa, the O-ring should be embedded in the metal groove to prevent the O-ring from being squeezed and deformed with the pressure change. In addition, the O-ring is easily damaged under high pressure. That is, under the action of high pressure, high-pressure gas molecules infiltrate into the O-ring for a long time. When the external pressure of the O-ring decreases instantaneously, the internal high-pressure gas molecules are easy to rapidly diffuse and break the O-ring. For example, the sealing O-ring at the valve seat. When the ball valve is rotated and opened, the internal pressure of the valve cavity will release the medium and make a huge sound. At this time, the O-ring is found to have been broken, indicating that the sealing performance of the ball valve has failed. It can be seen that in this case, it is recommended to use O-ring with high sealing performance for valve seat sealing, or replace the O-ring seal timely to ensure the normal operation of the valve pipe.
3. Failure analysis and treatment methods
Through long-term use and test practice, there are three comprehensive factors causing O-ring failure.
(1) Incompatible with media
In the daily ball valve product design, the selected O-ring is not compatible with the channel medium, which will cause corrosion, swelling deformation and fracture. Such problems will seriously affect the quality of ball valve products. For example, for the medium with high acid-base concentration such as nitric acid, sulfuric acid and sodium chloride, the application of O-ring shall be carefully considered when designing the ball valve.
(2) Fatigue failure
In the three-piece gas fire-proof ball valve used in the gas valve pipeline. If the pressure of the ball valve is 4.0Mpa and the actual pressure under the service condition is 6.3MPa, it is found that the O-ring seal at the support ring fails when the ball valve is installed in the pressure pipe and operated for a period of time. After analysis, because the actual working pressure range is larger than the fluctuation range of the pipeline system, and the pressure between them is very close, the opening and closing frequency is high, resulting in the O-ring reciprocating contraction and the O-ring reaching the specified life limit. It leads to fatigue failure of O-rings. In order to ensure the normal operation of the pipeline system, it is necessary to formulate a schedule for regular replacement of O-rings or reduce the opening and closing times of ball valves.
(3) Permanent deformation failure
Among all sealing materials used in ball valves, rubber O-ring is relatively lower in hardness than polytetrafluoroethylene (PTFE) and flexible graphite, but its resilience is higher than the former two. If it is applied to high-temperature and high-pressure valve pipes, the rubber will be distorted by heat and pressure, and it is easy to produce permanent deformation and failure. If the ball valve product is used in the low-pressure natural gas pipeline, the O-ring with 65 shore hardness is selected as the sealing element. After the product has been operated for a certain period of time, the O-ring at the valve seat seal is taken out and it is found that its surface is smooth, but its cross-section has changed into square groove shape without resilience, resulting in serious sealing failure. At this time, if the O-ring with shore hardness above 80 is replaced as the sealing element of the valve seat, the sealing performance of the O-ring is intact under the same conditions.
4. Conclusion
In the design and development of ball valves, when selecting O-rings as sealing elements, the influence of different working conditions such as temperature, medium and pressure and the change of working environment on the O-rings must be comprehensively considered. Secondly, the position, structure, installation and maintenance of the O-rings cannot be ignored. Only in this way can the service life of O-rings be extended, the service rate of O-rings be improved, and the normal operation of ball valve products in pressure pipes be ensured.
New Blog
© Copyright: 2025 Guangzhou JST Seals Technology Co., Ltd. All Rights Reserved.
Scan to wechat