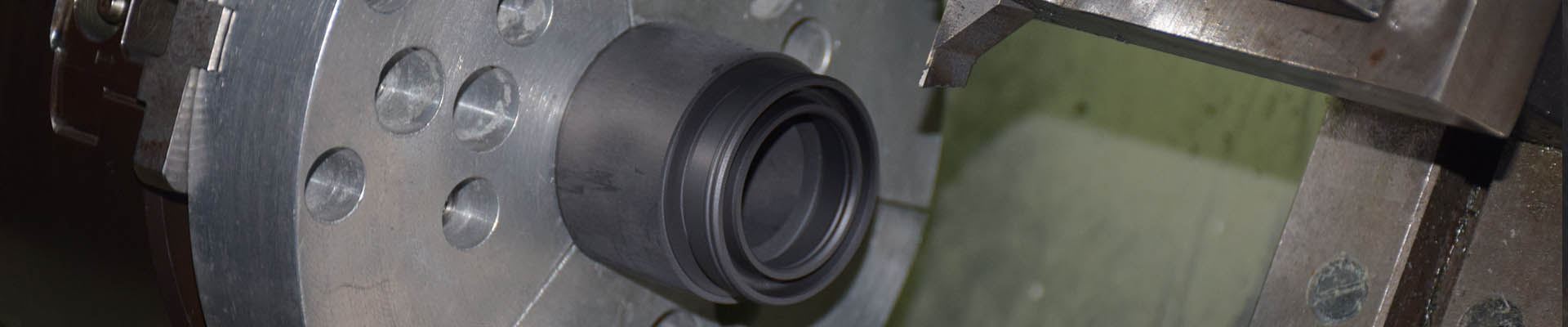
Why Nylon Ring Gasket in API 6A Gate Valve Factory Acceptance Testing is popular?
In the oil and gas industry, API 6A gate valves are critical equipment for high-pressure and high-temperature operations, where sealing performance directly impacts operational safety and efficiency. The Nylon Ring Gasket, as a key sealing component during valve testing, plays an indispensable role in factory acceptance tests. This article delves into its application scenarios, performance advantages, and testing standard requirements in API 6A gate valve evaluations.
------------------------------------------------------------------------
1. Stringent Requirements for API 6A Gate Valve Testing
Per API 6A standards, gate valves must undergo rigorous pressure tests before leaving the factory, including valve body hydrostatic tests, valve seat hydrostatic/pneumatic tests, and backseat tests. These tests validate the valve’s pressure-bearing capacity and sealing integrity under extreme conditions. Examples include:
Valve Seat Test: Bidirectional valves are pressurized in both directions, typically at 1.5 to 2 times the rated pressure. Hold times may extend to 15 minutes depending on PSL levels (e.g., PSL3G or PSL4).
Gas Test: Valves are submerged in a water tank to detect micro-leakages by observing bubble formation.
During these tests, the Nylon Ring Gasket must maintain stable sealing performance under high pressure, rapid cycling, and temperature fluctuations while avoiding damage to valve components.
2. Performance Advantages of Nylon Ring Gaskets
The unique properties of nylon make it an ideal choice for API 6A valve testing:
High Pressure Resistance and Elasticity: Nylon ring joint gaskets withstand test pressures up to 100 MPa (depending on PSL levels). Their elastic deformation capability ensures tight sealing by adapting to micro-gaps between the seat and body.
Chemical Corrosion Resistance: Nylon exhibits excellent resistance to corrosive media such as chloride-containing water or inert gases (e.g., nitrogen).
Temperature Adaptability: Within the typical API test medium temperature range (5°C–40°C), nylon gaskets resist brittleness or softening, ensuring test accuracy.
Reusability: Compared to metal gaskets, nylon’s low wear characteristics allow repeated use across multiple tests, reducing costs.
------------------------------------------------------------------------
3. Key Application Scenarios in Testing
Nylon gaskets are primarily used in the following API 6A gate valve factory test procedures:
Seat Sealing Test: Ensures leak-free performance between the seat and gate during bidirectional pressurization. For example, PSL3G seat pneumatic tests require the gasket to maintain a 15 MPa pressure for 15 minutes without bubble formation.
Backseat Test: Isolates the primary packing area to validate sealing performance in high-pressure gas environments.
Rapid Cycling Verification: The gasket’s resistance to compressive fatigue minimizes sealing failures during repeated valve actuation under full pressure differentials.
------------------------------------------------------------------------
4. Technical Requirements for Gaskets per Testing Standards
API 6A specifies clear criteria for sealing components:
Dimensions and Tolerances: Gasket geometry must precisely match seat groove designs (e.g., Appendix A recommendations) to prevent leakage due to dimensional deviations.
Hardness and Mechanical Properties: Compatibility with high-hardness valve materials (e.g., DD/EE grades) must be verified via Rockwell or Vickers hardness tests.
Environmental Compatibility: For austenitic stainless steel valves, test water chloride content must be ≤100 mg/L. Nylon gaskets should not swell or degrade under such conditions.
------------------------------------------------------------------------
5. Quality Control and Testing Optimization Recommendations
To ensure gasket reliability during testing, focus on the following:
Calibration and Precision: Pressure measurement devices must achieve ±2% of full-scale accuracy, with regular calibration (maximum 3-month intervals).
Test Medium Management: Use water with rust inhibitors for liquid media and nitrogen gas to minimize oxidation risks.
Failure Analysis: Investigate leaks by evaluating gasket installation orientation, surface damage, or material aging. Optimize selection using hardness test data.
------------------------------------------------------------------------
Conclusion
The Nylon Ring Gasket, with its superior performance, has become an indispensable "silent guardian" in API 6A gate valve factory testing. As industry demands for valve reliability grow, future advancements in nylon material modifications (e.g., enhanced temperature resistance or anti-creep properties) will further expand its applications. By adhering strictly to API standards and scientific testing protocols, manufacturers can ensure that every valve delivered operates safely under harsh conditions, supporting efficient energy industry operations.
New Blog
© Copyright: 2025 Guangzhou JST Seals Technology Co., Ltd. All Rights Reserved.
Scan to wechat